Good drainage is essential to a solid track structure, and drainage is accomplished
with proper ballasting and trackside ditches. High quality ballast is the key
to good track structure and overall stability. Failure to properly maintain
ballast will result in a gradual deterioration of the roadbed and subsequently
the degradation of the tracks. If minor drainage problems and clogged ballast
are left unchecked, they can lead to a serious maintenance problem and result
in lower safe speeds and increase the likelihood of derailments.
One measure of a railroad company’s financial health is the condition
of its tracks. A railroad with well-maintained, high-quality ballast shows
that the company has allocated its resources toward proper maintenance
and has a long-term outlook. By contrast, a railroad with poor ballast,
low rail joints, and uneven track has neglected the very foundation of
its track structure, and has cut corners for short-term gain. Excessively
dirty, weedy, and unkempt ballast indicate more serious problems, both
with the track structure and with the railroad company itself. When a railroad
is tight for cash and looking to trim expenditures, cutting funds for track
maintenance, particularly such projects as ballast renewal, is an easy
way to save money in the short term. But ignoring fundamental maintenance
is a gamble. In effect the company is mortgaging its future—and at a very
high interest rate.
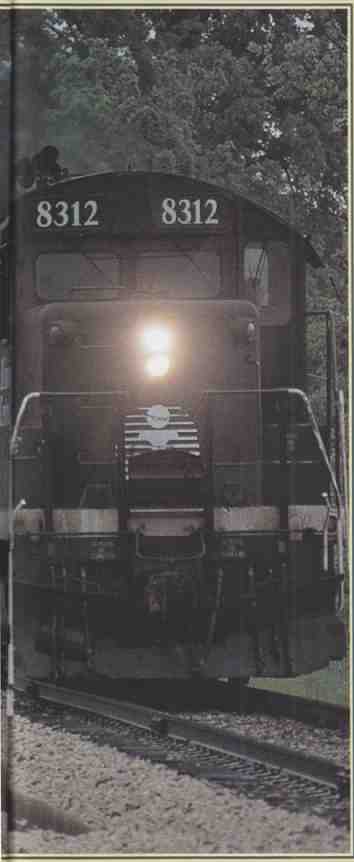
---ABOVE: Illinois Central’s Memphis to Grenada local carefully treads
through high water at Blanche, Mississippi, in April 1994. Proper ditching
and ballast maintenance is designed to draw water away from the track structure.
Flooding that brings water up to the level of the rail is extremely damaging
to the tracks.
Dirt Below the Surface
Fresh ballast is designed to drain water away from the center of the tracks
into ditches along the right-of-way. The ditches then carry the water away
from the roadbed. Most modern rail roads use crushed rock for ballast on
the mainline. It is the most expensive conventional kind of ballast, but
it has also proven to be the most effective. Crushed rock does a good job
of holding the track in place, and it provides excellent drainage.
Crushed stone flexes beneath the weight of a passing train while remaining
firm to hold the ties in place. Crushed stone is less prone to disintegration
and cementing than other forms of ballast, yet all ballast gradually becomes
fouled. Even stone ballast eventually breaks down and crumbles, becoming
abraded as a result of passing rail way traffic and the cyclical freezing
and thawing imposed by nature. Fine particles of abraded ballast, combined
with natural dust and dirt, and debris that has fallen from passing trains,
conspire to clog ballast, limiting its ability to drain water properly.
In addition, fouling matter in the sub- ballast and sub-grade tend to work
up through the good ballast, mix with water, and turn into mud. The mud
then effectively seals off the crib between the ties and acts as a dam,
preventing proper drainage and damaging the track.
Understanding how ballast clogs makes it easier to establish corrective
measures to solve the problem and restore tracks to good condition. Ballast
clogging is a vicious circle. As the ballast becomes clogged, its ability
to drain properly deteriorates, and water gets trapped in the ballast,
causing further damage that com pounds the situation. When the ballast
becomes waterlogged, the up-and-down action of the wheels of a train passing
on the track pumps water and debris from the sub-ballast, drawing it to
the surface and further soiling the ballast. When severe pumping occurs,
mud and water can be clearly seen around the ties and joints. This pumping
is aggravated in track sections with poor rail joints, where there is greater
movement caused by excessive pounding. As a result, tracks with traditional
jointed rail are more prone to this type of ballast deterioration than
modern welded rail, in which the joints are normally separated by as much
as 1,500 feet, instead of each rail having a joint every 39 feet. The problem
of clogged and cemented ballast is also more prone to occur on steeply
graded lines, where locomotives are constantly laying down sand on the
rails to gain traction. Heavily used railroads, such as heavy coal and
ore lines that carry a huge amount of material that can fall on the tracks,
suffer from more rapid ballast degradation than lines with cleaner traffic.
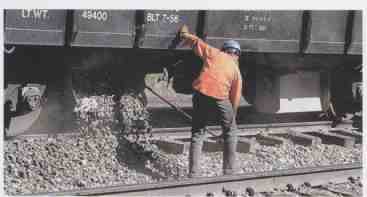
---ABOVE: A Montana Rail Link track worker manually dumps ballast along the
tracks at Muir, Montana, on September 21, 1994. Ballast cars are specially
designed to direct ballast on the tracks with chutes that can send the
Stone to either side of the rail. In this case ballast is directed outside
the rail.
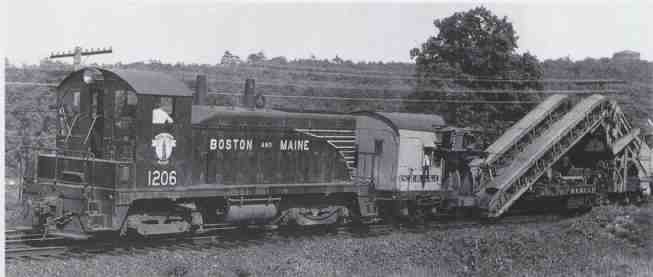
--- ABOVE: The Boston & Maine NW2 No. 1206 powers a traditional shoulder
ballast cleaner. The mechanized ballast cleaner is not a new concept; these
machines have been around for many years.
The depth of ballast and sub-ballast below it varies greatly from railroad
to railroad, depending on the type of traffic hauled, the age of the route,
and the type of ballast used. Traditional mainlines, particularly those
in the eastern and midwestern United States, tend to have the deepest layer
of ballast and sub-ballast, as a result of years of ballast renewal. One
conventional method of track renew al was to dump fresh ballast across
the tracks, and then jack the track—ties, rails, and all—through the layer
of ballast and tamp it down. In this scenario, the old ballast often becomes
sub-ballast. On some older lines, the combined layer of ballast and sub-ballast
runs more than 3 feet deep below the ties. Normally tracks should not be
lifted more than about 8 inches during ballast renewal if the tracks are
lifted higher than that, there is high risk of uneven settling, a condition
that may prove more troublesome than clogged ballast.
Ballast Cleaners and Undercutters
Repeatedly dumping ballast on tracks has its limitations. Every time ballast
is added to the tracks, the tracks get a few inches higher. This begins
to present problems at underpasses and other places with limited overhead
clearance. Ballast cleaning has long provided a solution for difficulties
with fouled ballast. In the days before mechanized track machinery, ballast
cleaning, like nearly all railroad maintenance, was accomplished by hand.
Men with picks and shovels re moved soiled ballast and ran it through a
sieve to shake out foreign matter. The ballast was then re placed manually.
It has been a long time since American railroads relied on this primitive
method of ballast cleansing. Since the steam era, machines have been designed
to do this job faster and more effectively than it could be done by hand.
Shoulder ballast cleaners are one such tool. These machines are designed
to clean the ballast along the edge of the tracks. Though this method cleans
only 30 to 40 percent of the ballast on the right-of-way and leaves the
majority of the bal last between the ties untouched, the theory be hind
it is that if the shoulder is cleaned and pro filed properly, the muddy
dams will be broken, allowing the natural drainage of the track to flush
unwanted debris and silt from the cribbing area between the ties.
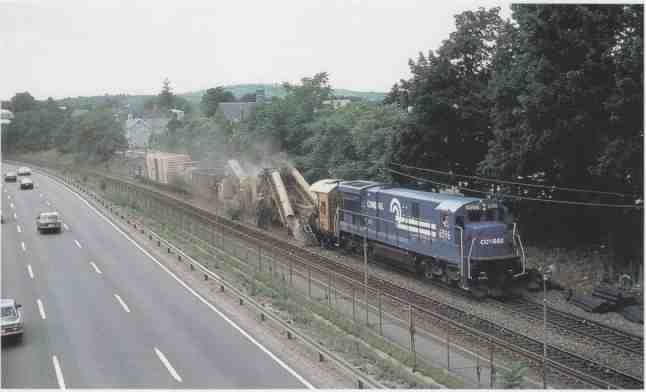
---ABOVE: Conrail’s C30-7A No. 6596 leads a Speno shoulder cleaner at Auburndale,
Massachusetts, on July 18, 1985, clearing the debris at the end of the
ties. Such debris causes damming in the cribbing between the ties. The
shoulder cleaner removes the dams to restore proper drainage, allowing
the ballast to function as it is intended.
A shoulder cleaning ballast machine rolls along on the tracks at a working
speed of just I to 2 miles per hour. It excavates ballast on both sides
of the track as close to the tie ends as it can with out the risk of damaging
them. The dirty ballast is deposited on a set of large vibrating screens
with in the machine. The screens serve the same function as the old sieves,
separating out the ballast from unwanted debris. The cleaned ballast is
re-deposited along the track, while the debris is sent by rotary conveyor
into hoppers that are hauled along by the train, or it is thrown a safe
distance from the tracks. Since dumping the debris back onto the right-of-way
is not always feasible, a bal last cleaning train might tow several hoppers
along behind it. The amount of work a ballast cleaner can do is limited
by the capacity of its hopper train. When the hoppers are filled, the train
must travel to a designated landfill to dump the debris before it can continue
its ballast cleaning. The rate at which the hoppers are filled depends
on the rate of ballast cleaning and how soiled the ballast has become.
A modern shoulder ballast cleaner manufactured by Loram excavates between
2 and 2.5 feet of ballast beyond the tie ends on either side of the track,
and reaches down 6 inches below the tie level. It also employs a scarifier
to the tie ends to remove the silt and mud that has dammed the crib area
and impeded drainage. Lo ram machines have built-in ballast regulators
and brooms that contour and trim the ballast to the correct profile after
it has been cleaned and re deposited along the sides of the track.
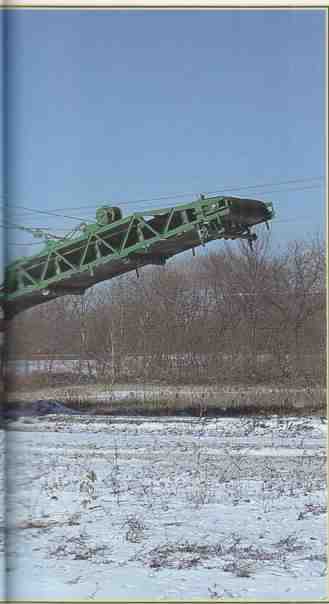
---ABOVE This shoulder cleaner uses its large cutting wheels to remove
ballast along the side of the track. The material is then sifted to remove
sand, dirt, and foreign matter that causes fouling, and the ballast is
dumped back on the tracks, while the fouling matter is thrown to the side
or dumped into hopper cars towed along with the cleaner.
While shoulder ballast cleaning can be the most cost-effective way to
restore proper drainage to a line suffering from clogged and contaminated
ballast, it has its limitations. Ballast can only be cleaned so many times
before it breaks down to the point where it is no longer effective. In
addition, ballast that has deteriorated to the point that it is completely
fouled cannot be effectively corrected by shoulder cleaning. In these cases
it may be necessary to remove the ballast with undercut ting machinery
and then completely replace it. Undercutting is also used where insufficient
vertical clearance prohibits the raising of tracks during ballast renewal,
such as on lines that pass through long tunnels or through urban areas
with numerous overhead bridges. In these instances, under cutting may be
the only effective way to restore proper drainage.
Some undercutting machines use a continuous chain placed below the tracks
to scoop away ballast and debris. Others use a large rotary wheel to dig
a lineside trench and a bar placed below the tracks to remove fouled ballast.
As with ballast cleaners, an undercutter can deposit the material into
hoppers with a conveyer or distribute it well away from the tracks to keep
the old ballast from interfering with drainage. Since an undercutter does
not return any material to the roadbed, it tends to fill hoppers more quickly
than ballast cleaners. While a ballast cleaner just deposits fouling material
in the hoppers, an undercutter deposits everything it scoops up. Modern
ballast machines sometimes combine undercutting and ballast cleaning functions.
Harsco Track Technologies’ Trac-Gopher (Model GO-4S) is a 100,000-pound
undercutter designed for mainline and switch/highway-crossing work. Using
a 12-foot, 7-inch trenching wheel, it is designed to cut a 20-inch-wide
trench up to 34 inches deep alongside the track. The trenching wheel can
be laterally adjusted, allowing the trench to be located anywhere from
immediately adjacent to the ties to up to 9 feet from the center of the
track. Once a preliminary trench is excavated, a 15- foot-long, 6-inch-deep
cutting bar is placed below the tracks to remove ballast from below the
ties. The bar is adjustable to allow undercutting from 6.5 inches to 2
feet, 3 inches deep. The undercutter is powered by an eight-cylinder General
Motors diesel engine that runs at 1,200 rpm, generating 364 horsepower.
The undercutter runs on four 30- inch wheels and has 15,000 pounds tractive
effort, enough to tow up to four 100-ton loaded ballast cars on level tangent
track. Undercutting spoil is transferred to a conveyor that can throw it
as much as 45 feet from the track, or deposit it in ballast cars. While
the Trac-Gopher has a travel speed of up to 25 miles per hour when it isn’t
undercutting, its working speed is just 2 to 10 feet per minute. At this
speed, it can undercut a maximum of 600 feet of track per hour. The machine
itself is 15 feet tall, 10 feet, 6 inches wide; and 40 feet long. Unlike
traditional undercutters that had minimalist wire-frame cabs, the Trac-Gopher
has a comfortable, completely enclosed operator’s cab. It is relatively
spacious inside, and is insulated, pressurized, and equipped with a heater
and an optional air conditioner.
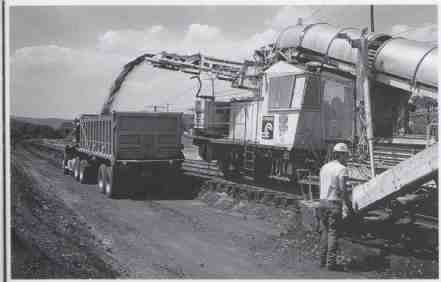
---ABOVE: Conrail’s Dirt Devil undercutter chums away at Milepost 81 along
the Boston & Albany. In the 1980s, many lines used specialized machines
such as this one to increase their mainline clearances in order to accommodate
taller trains.
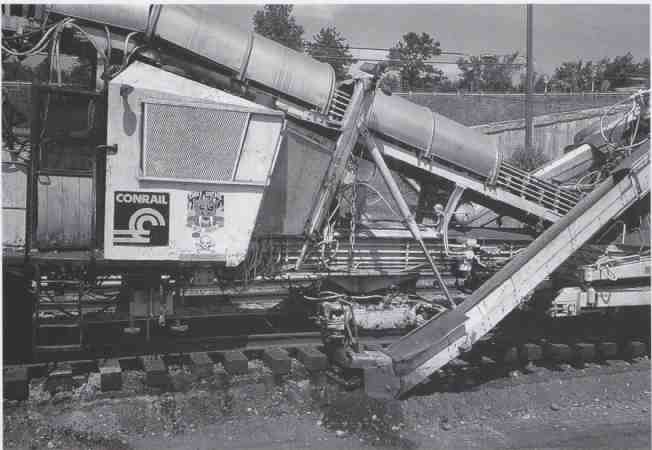
---ABOVE: The undercutter uses an excavating chain placed below the tracks
to remove ballast and soil from beneath the ties. As the machine moves
forward (to the left in the photo), the debris is dropped in a hopper (seen
on the right), which sends it away from the tracks via conveyor belt.
In addition to ballast renewal considerations, railroads may decide to
undercut track as a way to increase clearances. In situations where it
is physically difficult, prohibitively expensive, or politically impossible
to raise vertical clearances, undercutting is an attractive alternative
for improving clearances on the line. In the mid-1960s, the Pennsylvania
Railroad chose to undercut portions of its Philadelphia-Harrisburg mainline
to better accommodate tri-level autoracks. The line is electrified with
overhead catenary, energized with 11,000-volt alternating current. Prior
to its clearance improvement project, Pennsylvania Railroad experienced
occasional difficulties with wires coming into contact with the tops of
new automobiles on auto-carrying freight cars. (This was in the days before
protected covered autoracks, and the cars simply ran out in the open.)
One can just imagine the spark show when brand-new Chevys or Fords hit
the wires! Undercutting was required where low overhead bridges forced
the level of the wires too close to the tops of the cars.
In the mid-1980s, American railroads began to take advantage of deregulation,
spurring the in creased operation of double-stack container trains. At
the same time, concerns from automobile manufacturers about vandalism to
new cars riding in open autoracks led to the development of tri-level covered
autoracks. Since these new types of railroad cars were several feet taller
than most conventional cars, many railroads undertook massive clearance
improvement programs to accommodate them. Again, undercutting was often
the preferred option.
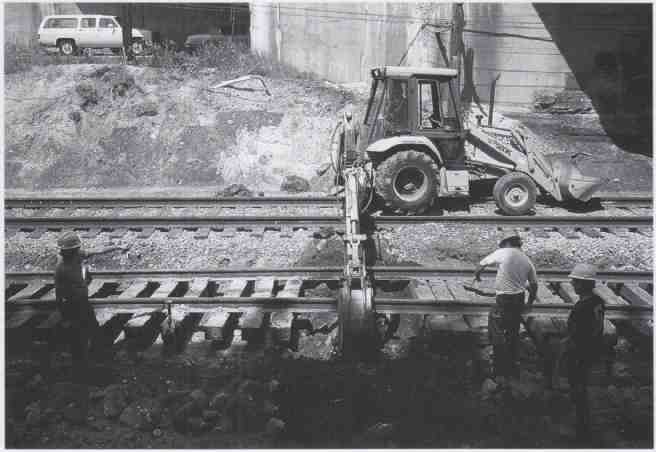
---ABOVE: Before the undercutter can get its cutting chain below track level,
a backhoe removes ballast, and the tracks are jacked up. Here at Milepost
81 on the Boston & Albany route, the tracks are being lowered about
1 foot to increase the vertical clearance and permit the operation of tri-level
covered autoracks and other tall cars.
Ballast Trains
Fresh ballast is often needed during track work to replace soiled ballast
or to replenish existing ballast, or it is laid down in preparation for
new or relocated track. Ballast is typically quarried on line and distributed
around the railroad in specially assigned ballast trains. While railroads
may designate old coal hoppers or ore jennies for the task of transporting
ballast, often they utilize more specialized equipment. Air-actuated side-
dump cars are used to distribute large quantities of ballast to the sides
of the right-of-way. The Difco dump car is a common type of commercially
produced air-actuated dump car. For general distribution, specialized ballast
hoppers are employed to haul and dump the stone. Since ballast is extremely
heavy, ballast hoppers tend to be lower, shorter, and more durable than
hoppers used for coal. Ballast hoppers are also designed to distribute
their load along the tracks, and simple coal chutes are not the most effective
way of doing this. A good ballast hopper can easily control the amount
and direction of ballast dumped, and directing the flow of ballast to either
inside or outside the rails is an important function of the ballast trains.
Traditionally, ballast was spread along the tracks very slowly, usually
no faster than walking speed. As the ballast train crawled along, employees
walked beside the train and distributed the ballast by opening and closing
chutes as needed to regulate the flow.
Technology is catching up with convention al methods. In 2000, the Herzog
Contracting Corporation, one of the leading lessors of ballast equipment,
introduced a modern high-tech bal last delivery system known as the Programmed
Linear Unloading System, or PLUS train. Where conventional ballast trains
delivered ballast at less than 5 miles per hour, Herzog’s PLUS train can
dump ballast with precision accuracy at speeds up to 20 miles per hour.
This space-aged ballast train uses modern computer and Global Positioning
System technology to do its job. A skilled Herzog technician rides ahead
of the PLUS train with a railroad representative, ideally a road foreman
or track maintenance supervisor, and takes detailed notes as to the desired
location and quantity of ballast needed. This information, along with the
location of bridges, switches and obstructions that may interfere with
ballast distribution, is logged on-site into a laptop computer. It is later
downloaded to a computer on board the train, which uses the in formation
when applying ballast. The hopper door controls are extremely sensitive,
and de signed to carefully regulate the flow of ballast to the track. The
computer on board the train takes the speed of the train into account when
delivering the ballast, adjusting the door openings to compensate for the
speed. If the train is moving faster, ballast needs to be dumped at a greater
rate than if the train is moving slowly. This system minimizes problems
caused when a ballast train slows abruptly during ballast spreading. The
ballast doors on the PLUS train are larger, and open and close up to five
times faster than on more conventional equipment, which permits the train
to dump its load much more quickly. A PLUS train of 50 100-ton hoppers
can deploy its entire load in less than an hour. Such a time saving is
a great advantage to modern railroads with limited time windows available
for track work. Since the entire train is automated and the ballast sites
have been predetermined, it is unnecessary for railroad personnel to be
on the ground, offering an additional saving for the railroad. Like other
modern track-monitoring equipment, the PLUS train’s survey system records
the information and holds it for future ballasting needs. This allows a
railroad to determine if a particular stretch of track is using an excessive
amount of ballast over time, and appropriate remedial action can be taken.
Herzog hopes that its new train will win favor with American railroads
by its increased productivity and cost savings.
Ditch Diggers
Directing water away from the track is a routine yet extremely vital aspect
of a railroad’s maintenance program. Standing water undermines track stability,
and as a result, drainage ditches are a standard part of railroad construction.
Traditional ditching methods were time-consuming, labor-intensive, and
expensive. The work required large gangs of men along with steam shovels
and other equipment. As railroad technology progressed, ditching moved
from conventional manual methods to mechanization. One of the first mechanized
ditching tools was the Jordan Spreader, discussed in detail later in the
section. Though the Jordan was an excellent tool in its day, and some lines
still use them, new more advanced machines have superseded the Jordan Spreader
as the ditching tool of choice. Because today’s railroads demand maximum
track utilization, making maintenance windows precious commodities, specialized
ditching machines have been developed that operate much faster, more cheaply,
and more accurately than more conventional machines.
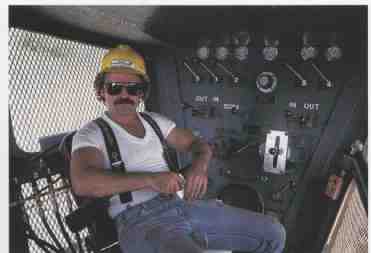
---ABOVE: The operator amenities in Conrail’s Dirt Devil undercutter are minimal,
but the controls are relatively straightforward.
The primary objective of a ditch digger is to move away earth and water
while profiling the land to create a drainage ditch. The ditch is designed
to lower the water table around the tracks by drawing water away from the
roadbed. To make the best use of a modern ditch digger, facilitate fast
ditch digging, and minimize its time on the mainline, rail roads will prepare
a site in advance and clear away debris. Anything that might damage, clog,
or delay ditch digging machines is removed by workers and machines on the
ground. This includes, for ex ample, old crossties, fragments of broken
rail, large rocks, and brush.
=====
Conrail Ballast Express
Some railroads paint ballast fleets distinctively to distinguish them
from revenue service cars. Union Pacific’s ballast cars are treated with
a forest green livery, Amtrak’s are a brilliant safety orange, and Conrail’s
were a light gray that almost matched the color of the stone they carried.
While many railroads assigned any surplus motive power to ballast service,
a few have designated locomotive fleets for work or ballast trains. Conrail
obtained much of its ballast from a quarry in West Springfield, Massachusetts,
along the old Boston & Albany route. Ballast quarrying is strictly
seasonal business in New England because of the cold and sometimes snowy
winters, so most of Conrail’s ballast was delivered in the spring, summer,
and early autumn. In season, a train or two of ballast would be loaded
every day, and then hauled over Washington Mountain for distribution on
the rest of Conrail’s system. This was an especially difficult pull, involving
a winding 1.67 percent climb between Chester and Washington. Conrail locomotives
would slow to a crawl trying to haul the ballast trains over the hill.
While most trains made it without serious problems, all too often a heavy
ballast train would stall a few miles west of Chester, Massachusetts, as
it entered the reverse curves at Milepost 129.
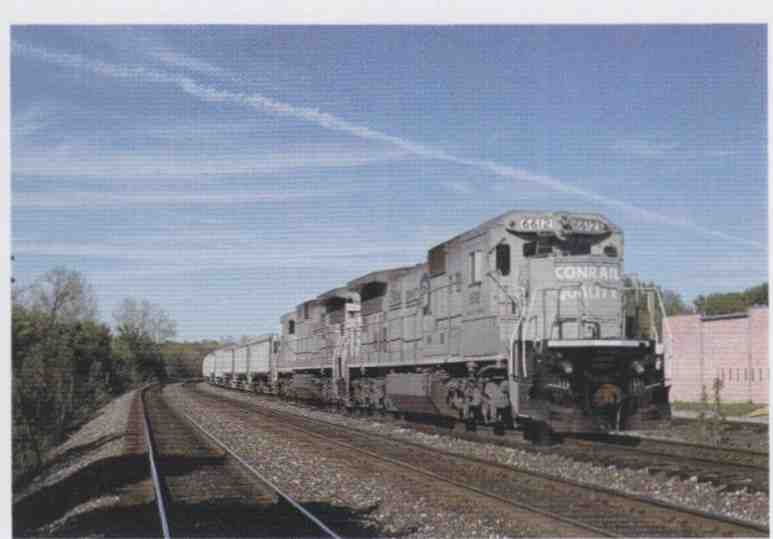
---ABOVE: A pair of Conrail’s unique General Electric C32-8s, in Ballast
Express paint, work on the former Pennsylvania Railroad at Latrobe, Pennsylvania.
The 10 Conrail C32-8s were the only examples of this type of locomotive.
Conrail reassigned the fleet to work train service in the late 1990s.
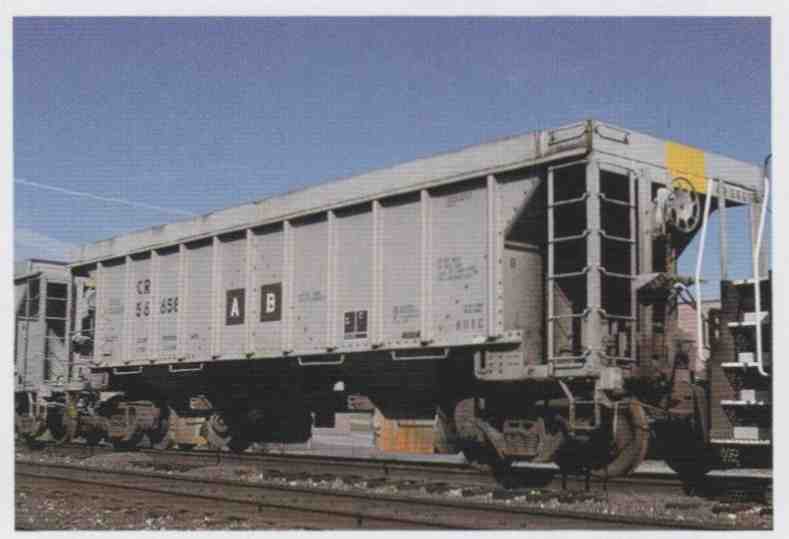
---ABOVE: This Conrail ballast hopper has remote-controlled ballast doors
that permit rapid spreading of ballast along the right-of-way. The car
can carry up to 200,000 pounds of stone. Notice how the chutes are aimed
to direct ballast to either side of the rail.
For many years, Conrail’s ballast trains warranted the same types of six-axle
locomotives used by the other Conrail trains on the B&A. Toward the
end of Conrail operations, before the railroad was divided by Norfolk Southern
and CSX, Conrail reassigned its fleet of 10 General Electric C32-8s to
Boston Line ballast service. These unique locomotives were delivered to
Conrail in 1984 and spent much of their careers working on the Boston Line.
The locomotives were unusual for several reasons: They were the only C32-8s
ever built and they used a 12-cylinder FDL engine, instead of the far more
common 16-cylinder FDL engine. Externally they had the Classic Dash 8 car
body, with curving contoured cabs—a body style that was in production for
only a few years. In the mid I 990s these locomotives were repainted from
Conrail blue to a distinctive gray scheme and lettered for Ballast Express
service. For several years they were regularly assigned to ballast work
and hauled loaded stone trains all over the system. When there wasn’t ballast
work for them, Conrail used them on other Boston Line services. CSX also
assigned some locomotives in work train service, painting them a bright
safety orange and assigning them to ballast trains and other maintenance-of-way
duties.
=== ===
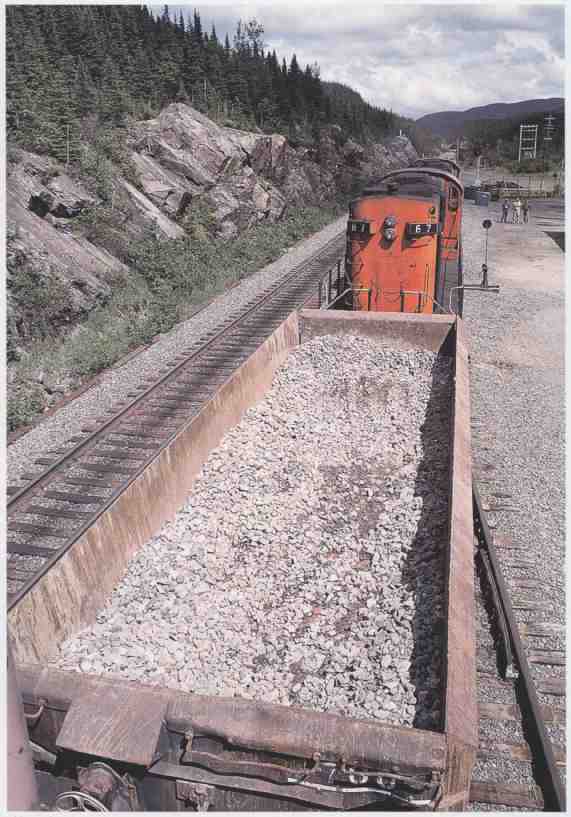
--- ABOVE: This work train on the Cartier Railway in northern Quebec offers
a good view of a dump car used to distribute ballast. It can dump to either
side of the track. Because of its isolated nature, the Cartier still does
most of its maintenance with traditional rail-based equipment.
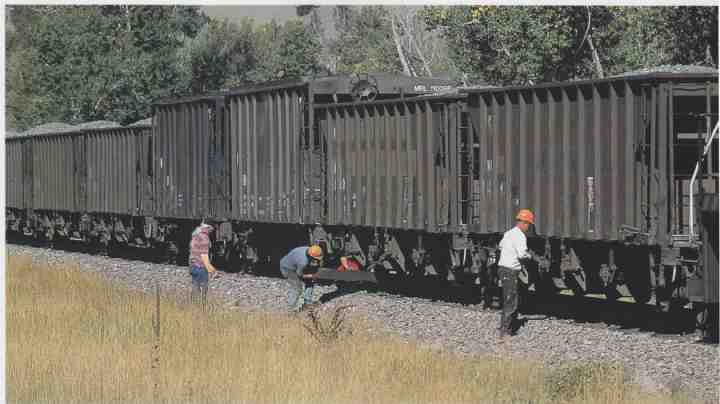
--- ABOVE: A trackman on the Montana Rail Link adjusts the traps on loaded
ballast cars in preparation for spreading the stone on the tracks.
Loram, the maintenance equipment contractor known for its undercutting
and rail grinding services (see section 5), also offers one of the most
modern mechanized ditching machines. This able machine is named after the
badger, a mammal known for its rapid burrowing ability. A badger can dig
a hole with its paws much faster than a man could with his hands; likewise,
Loram’s Badger ditch digger is designed for greater speed and efficiency
in digging trackside ditches. The Badger is a self-propelled machine that
can attain a travel speed of 45 miles per hour, which gets it over the
railroad fast when moving between work sites. It features two adjustable
arms for digging. One carries a high-speed digging wheel to sculpt the
ditch, and the other is a conveyor to remove earth and water from the digging
site. The Badger can dig a ditch between 6 and 18 feet from the track center,
and can cut down to 4 feet below the rail level. It can profile a ditch
to most specifications required to improve track drainage. Many ditches
can be dug with a single pass of the Badger, but some may require multiple
passes, especially more complicated terraced ditches. The Badger works
much faster than older machines, meaning more works gets done in less time.
At its best, the Badger can move as much as 1,000 tons or 500 cubic yards
of earth and water every hour. The conveyor can be aimed to deposit ditch
waste up to 35 feet from the tracks, or into air-actuated side-dump cars
carried along with the digging ma chine. The method of waste disposal depends
on the area being ditched. Drainage problems often occur in deep rock cuts,
and in such constraining environments, it is more convenient to use the
dump cars for waste removal.
Unlike other elements of track geometry and roadbed design, ditch digging
is a fairly inexact process. The theory behind ditch placement doesn’t
always work the way the railroad hopes it will. A ditch may function adequately
under normal circumstances, draining runoff away from the roadbed and keeping
the right-of-way sufficiently dry, but be inadequate for more extreme conditions.
For example, railroad ditches have to accommodate a lot more water during
heavy rains than they do on normal days. If they fail, tracks can flood
or wash out. Washouts are relatively rare these days, and accidents caused
by washouts even rarer. They can still happen, however, so maintenance
crews must be on their toes, keeping drainage systems up to par and ready
for the big 10-year or 50-year flood. In assessing ditch capacity, routine
drainage and extreme flooding need to be considered separately.
When planning ditches along its lines, a rail road needs to weigh the
costs of ditching against the risk and impact of severe floods. In some
cases, no amount of trackside ditching will help, and in these situations
other alternatives must be considered. For example, railroad lines that
cross the Sacramento River Delta and flood plain are built on trestles,
rather than embankments, even though most of the time the area below the
tracks is bone-dry. When the flood does come, the trestle is the only way
to go.
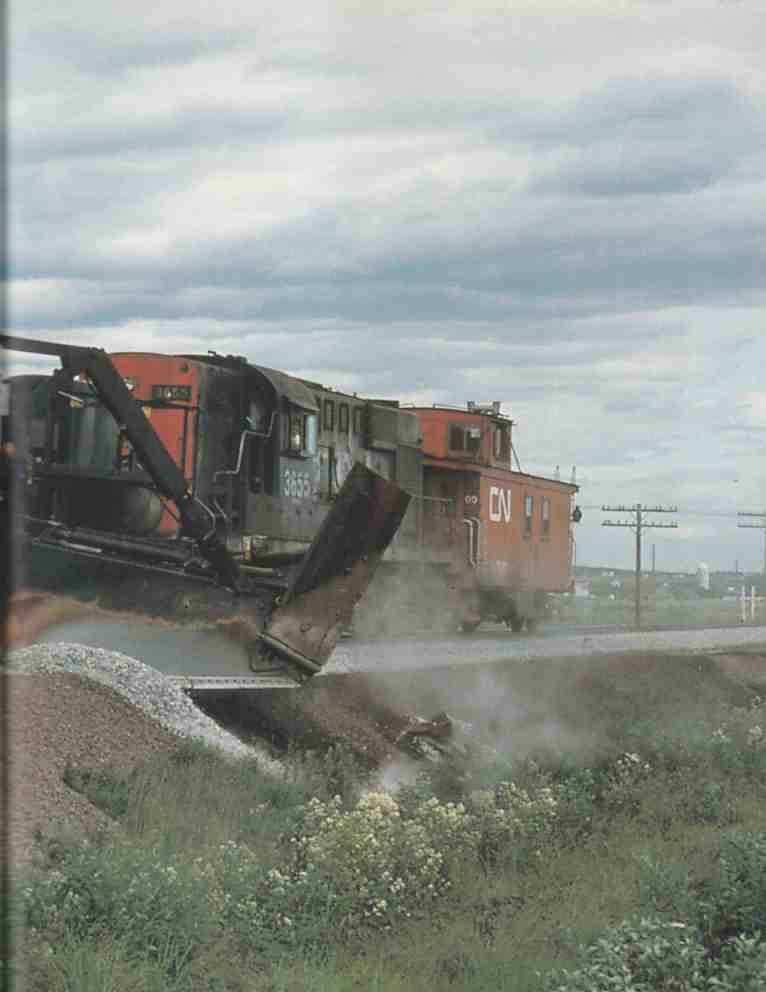
---ABOVE: On July 12, 1978, a Canadian National Jordan Spreader shapes
ballast as it is shoved along. The Jordan’s adjustable wing was designed
for this type of contouring work. Versatility was one of the Jordan’s great
attributes; this one machine could be fitted with more than a dozen different
attachments.
Jordan Spreaders
It is difficult to find a piece of equipment that is as universal and
as useful for railroad maintenance as the Jordan Spreader. It is one of
the oldest types of maintenance machines employed by modern railroads,
and at one time it was among the most common. While it has largely been
sup planted by more modern, specialized maintenance equipment, the traditional
Jordan Spreader can still be found on many railroad lines. The Jordan can
work as a ditching machine, a ballast regulator, and a heavy snowplow.
It combines all these tools in one rugged, adaptable, low-tech piece of
equipment. The Jordan is one of the last relics of the steam era still
found on American railroads.
The Jordan Spreader is named for its inventor, Oswald F. Jordan, a one-time
roadmaster for New York Central’s Canada Southern Lines. In 1905, he left
the railroad, and applied his years of experience to developing, building,
and marketing a track maintenance tool that was superior to anything else
available at the time. In the first few years, Jordan contracted the job
of building his distinctive machines to various railroad shops. It wasn’t
until about 1911 that Jordan opened a factory and began manufacturing the
spreaders himself. Jordan’s factory was located in East Chicago, and it
was always a relatively modest facility. For more than five decades the
company built spreaders and snow- plows, until the company was acquired
by Jackson Vibrators in 1964. More than 1,100 Jordans were sold to railroads
all around the country and Canada. Jackson-Jordan was one of the predecessors
of today’s Harsco Track Technologies.
The Jordan Spreader is a simple machine with relatively few moving parts
and virtually no complicated machinery. As a result, it doesn’t require
much maintenance, it can be largely ignored for months at a time, and yet
be ready to go at a moment’s notice. It shares many qualities with older
snowplow de signs (discussed in greater detail in section 7). The basic
Jordan has a pivoting front-mounted plow that can be angled to direct the
material it is pushing to either side of the tracks. Each side of the machine
is equipped with large adjustable wings that can be ex tended and locked
into place. The wings are hinged near the front of the machine, and they
are adjusted by large cylinders. Most Jordans built before the 1950s used
air-actuated pneumatic cylinders, later machines were hydraulic, and they
carried a small diesel engine on board to operate the hydraulic pump. A
variety of different attachments could be applied to the Jordan’s plow
and wings, which was one reason for its popularity and versatility. Customized
plow blades could be used to match the needs of the railroad. Many Jordan
Spreaders came equipped with large snow-service plows and were intended
as snowplows.
The Jordan, once used commonly as a ditching machine, is rarely used for
ditching today. Many railroads had distinctive ditch-cutting blades that
were designed to create a specific profile. Since the spreader has no power
of its own, a locomotive has to shove it from behind in order for the spreader
to do its work. The Jordan must be stationary when it is set up for ditching,
and once it is ready, a loco motive will shove it along at about 5 miles
per hour. The machine’s operator can make minor adjustments, raising and
lowering the wings with the cylinders, as required by the railroad’s grading
pro file. Watching for signs along the right-of-way and taking cues from
his experience, the Jordan operator keeps his eyes on the wings, while
remaining in close communication with the locomotive engineer pushing him
forward. In the days prior to radios on trains, this was a tricky business,
and the Jordan operator, like most trainmen of the period, had to be well
versed in nonverbal communication. Basic tasks can be accomplished with
just a single well- planned pass of the Jordan, but more complicated ditching
routinely requires repeated passes over the same area, with some adjustments
to the wings and blades with each successive pass.
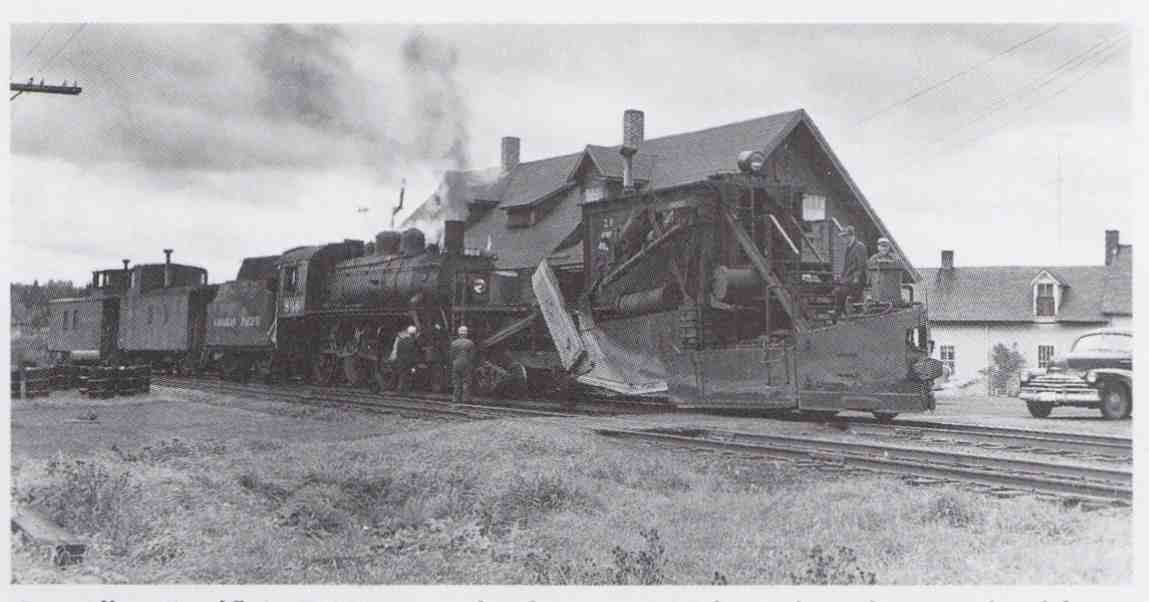
---ABOVE: Canadian Pacific’s D10 Ten-Wheeler No. 806 is assigned to work
with a Jordan Spreader. This photo was made at Debec Junction, New Brunswick,
on October 3, 1956.
The Jordan’s natural advantage over digging equipment that does not ride
on the rails is the uniformity and stability afforded by the guiding tracks
and the machine’s relatively heavy weight. This benefit is especially valuable
when plowing or ditching on curved track, as the Jordan can easily maintain
a consistent profile. A late-era Jordan Type A weighs about 130,000 pounds,
which means it is unlikely to be disturbed by normal ditching duties. The
blades are made of extremely tough manganese alloy steel, and are resistant
to breakage.
Like the Titanic, however, the Jordan is not invincible, and the operator
must know the limits of his machine. An efficient operator will let the
Jordan do its work, allowing a reasonable margin of safety, without being
overly cautious. One thing the Jordan is not suited to tackle is large
rocks. These are likely to damage the machinery and are best re moved before
the spreader is set to work.
The early Jordan Spreaders didn’t have a protective cab for the crew.
Later machines had a small centrally situated cab. Eventually the cab was
enlarged and moved forward to give the operator a better working environment
and improved visibility. The four models of spreaders built in later years
were the Standard, a relatively small machine discontinued in the 1960s
the Roadmaster, which was a little larger the Type A Jordan; and the Type
J Jordan. One of the biggest changes in the basic design of the Jordan
Spreader was the introduction of hydraulics in the 1950s. Still, even after
hydraulics were offered, Jordan continued to build the older pneumatic
style of machines. In the world of modern track machinery, where electrical
and hydraulic control are the norm, an air-controlled machine seems terribly
primitive.
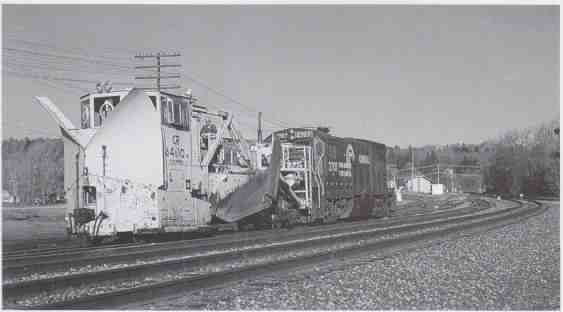
---ABOVE: Conrail’s Jordans were painted bright safety yellow and equipped
with large snow-service plows. This Jordan is seen along the former Erie
Railroad Buffalo Line at Attica, New York, on May 8, 1988.
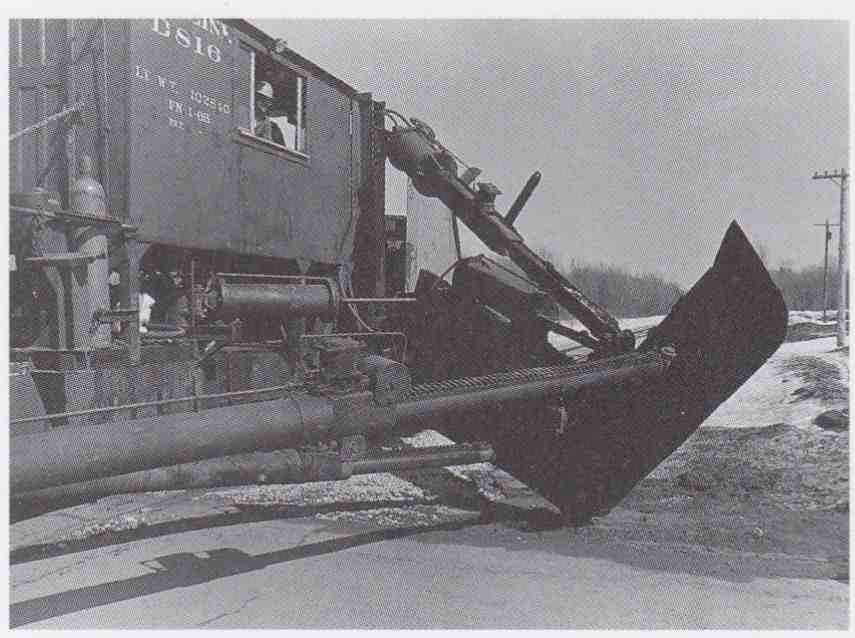
---ABOVE: On March 23, 1973, a Soo Line Jordan has its wing extended and
lowered into position, ready to clear out a ditch along the right-of-way.
It is a traditional air-actuated machine dating from the steam era. Some
railroads still use Jordans despite the development of more modern equipment.
Prev. | Next
Top of Page | Article
Index |