One warm summer evening in 1984, some friends and I had the good fortune
to witness a rail grinding train roll through the Amtrak station in Springfield,
Massachusetts. The train had been working all day up on the Hill,” the old
Boston & Albany mainline in the Berkshires of western Massachusetts. As
the train crawled through the station against the current of traffic on the
Number I track, I inspected the machinery. The grinder consisted of several
cars coupled together. On the sides of the machine were stored dozens of circular
grinding stones, tools, and related equipment. The grinder was painted an orange-yellow
color, but after days and days of hard work, the entire machine was covered
in slate-colored dust and grime. Toward the back of the machine, set upon it
like a permanent fixture, was a bedraggled track worker. After a long hot humid
day grinding track in the Berkshires, he—like the machine he was working with—
was totally covered in grime. It seemed that no part of him was free of it.
Although I didn’t take his photograph as the train rolled by, I will never
forget the expression on his face. Exhausted and ambivalent, he was as impassive
as a shell-shocked war veteran. He looked like he had seen it all. Once the
rail grinder had cleared the mainline the freight trains, many of which had
been held during the day’s work, began to roll, one right after another through
Springfield station. Why, I wondered, was it so important to subject men and
machinery to the rigors of rail grinding?
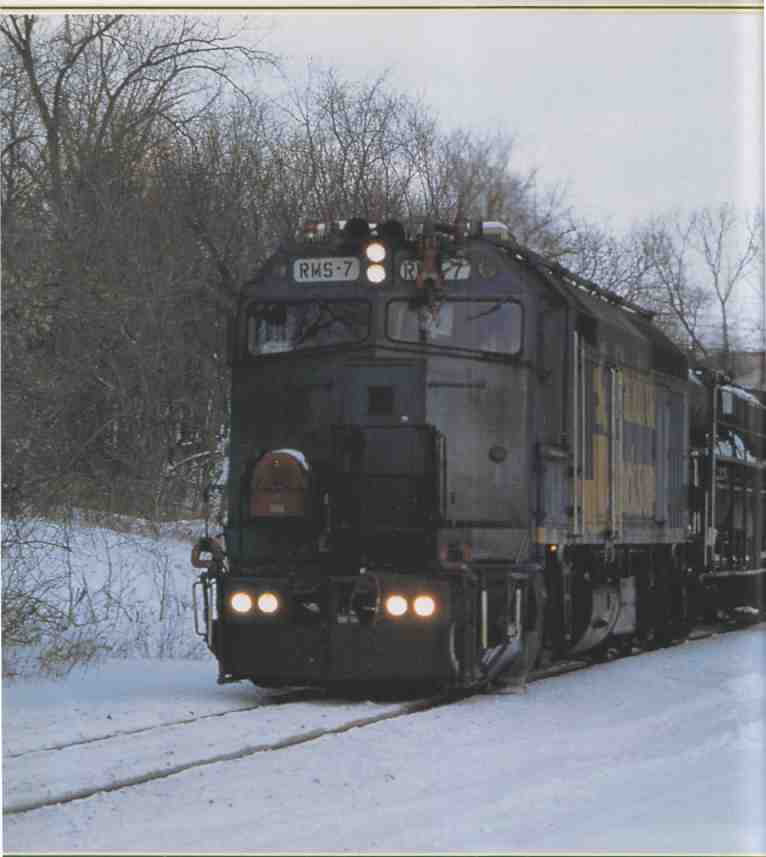
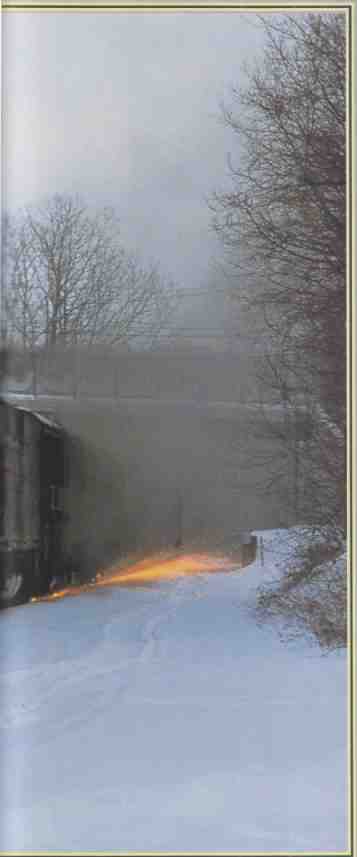
ABOVE: A Pandrol-Jackson grinder profiles Delaware & Hudson tracks
at West Waterford, New York. Rail grinding is an essential part of maintaining
healthy rail conditions by improving the rail profile after excessive wear.
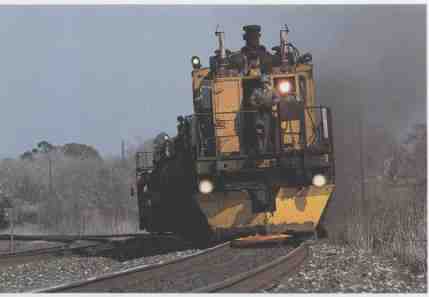
ABOVE: Rail grinding is hard work, and serious business. Properly profiled
rail can save a railroad lots of money by extending the rail life and reducing
wear to other track components. Grinding heavily traveled lines, particularly
in curves, is especially important. Loram grinder No. 6 profiles a curve
at Wiermar, Texas, on February 8, 1992.
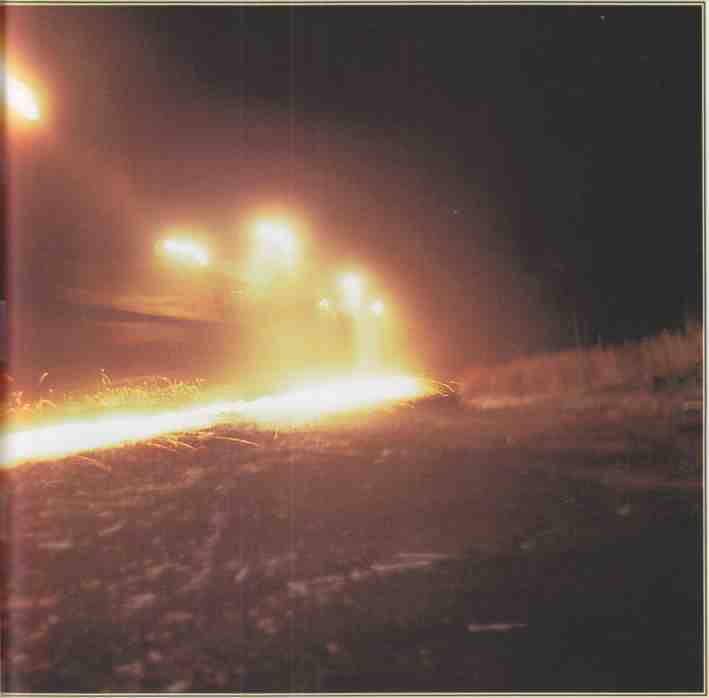
ABOVE: Alert the authorities—the aliens have landed! No, it’s just a
rail-grinding train at night. All too frequently, concerned citizens alert
police and fire departments when they see the nocturnal fireworks of a
rail grinder. With as many as 120 grinding stones shaving steel simultaneously,
a grinder can be quite a show.
Steel wheels on steel rails is the story of railroading. Yet, steel wheels
inflict terrible damage on the rails. Every inch of the way, wheels are
fighting the rails that guide them; they grind, flat ten, and distort as
they roll along. Wheels cause destruction at every point where they contact
the rails. It may not be obvious after a single passing of a train, but
the damage is there. The more wheels that roll over rails, and the greater
the load those wheels support, the more damage is done. The contact between
rail and wheel damages the wheels as well, and as the wheel is worn, it
proves more and more damaging to the rail. On tangent track, locomotives
have a tendency to hunt (travel rhythmically back and forth), which causes
unevenness in the rail. Over time, the effect is comparable to traveling
on a bumpy dirt “washboard” road. Curved track suffers from additional
problems. As wheels take a curve, they place great pressure on the outside
rail, grinding away the head and distorting its shape.
On a busy mainline, maintaining healthy rail conditions is very important
business. High levels of rail wear leads to a variety of problems that
con tribute to a general deterioration of the track structure. This wear
is also damaging to passing trains and lowers the overall efficiency of
the railroad. On traditional lines with jointed rail, it was relatively
easy to exchange sections of damaged rail one piece at a time. Steel rails
are very expensive, however, and exchanging them is both costly and time-consuming.
On a modern railroad, the costs of changing rail are an even greater concern.
Since most modern mainlines employ continuous welded rail, exchanging sections
is extremely time-consuming and labor-intensive, and requires the line
to be shut down for many hours at a time. Furthermore, the railroads have
eliminated superfluous, redundant, and underutilized tracks and facilities,
and as a result they have far less mainline today than ever before—not
just fewer routes, but less track. Lines that once had double-track mainlines
now often are just single track. This one track, using strategically placed
passing sidings, carries all the tonnage of the entire line. When the track
is out of service, the railroad stops and waits for it to be restored.
This scaled-down network, combined with the increases in railroad productivity
and the ever-greater amounts of traffic, presents greater problems for
routine maintenance. Rail wear is higher, yet less time is avail able to
take the track out of service to correct it. This doesn’t mean the railroads
are being run into the ground. Instead, modern maintenance pro grams, including
rail grinding, have greatly reduced the amount of time needed for railway
maintenance. Rail grinding technology has evolved to actually prevent problems
before they happen.
Rail grinding offers a practical solution to rail replacement. It can
greatly increase the useful life of rail by improving the rail profile
to facilitate a lower wear rate, prevent fatigue, and eliminate surface
defects, while controlling damage from wheel hunting. Rail grinding minimizes
the destructive forces caused by wheel-rail contact, which in turn limits
the damage to other track components. It reduces the accumulation of steel
particulates and other dirt that result from high track wear, thus ex tending
the life of ballast. Also, proper rail profiling reduces wear to fasteners
and joints. A better rail profile increases efficiency through improved
contact between wheel and rail, resulting in lower fuel consumption, a
smoother ride, and less noise.
Modern rail grinders use specialized rotary grinding stones, powered by
either electric or hydraulic motors, to re-profile worn rail. Various grades
of stone are used, the coarsest for the heaviest work, and the finest for
finishing work. The life span of the grinding stones is relatively short,
typically requiring replacement every two or three hours. Sometimes stones
break during grinding and need immediate replacement. The high frequency
of stone replacement requires that the stones be easily removed from the
grinders, a procedure that is repeated more than 100 times a day on a large
production grinding train.
Each rail grinding train has banks of grinders that are carefully positioned
by a computer to obtain the desired profile. Since the purpose of grinding
is to prolong rail life and improve rail road efficiency, rail grinders
are designed to shave as little metal off the rail as possible. The amount
of metal removed is measured in 100ths or 1000ths of an inch. In order
to ensure that the proper amount of metal is removed, the grinding motor
speed is carefully regulated. The working speed of the grinding train also
has to be closely regulated and may be adjusted by tenths of a mile per
hour. Although the grinders are capable of fairly high travel speeds, they
move at just 1.5 to 15 miles per hour when working.
Rail grinding philosophy has evolved in the last few decades to reflect
the changing needs of modern railroads and to take advantage of new technologies.
New maintenance considerations have been developed to deal with increased
train weights, higher tonnage, new types of rail alloys, and the introduction
of three-phase alternating current locomotives with extremely high tractive
effort and more effective dynamic braking capabilities. In the last decade,
railroads have moved away from traditional corrective rail grinding practices
and implemented progressive preventive strategies. Corrective rail grinding
was aimed at repairing existing rail defects and was usually performed
on a routine calendar basis. The rail grinding profiles were typically
established by local railroad staff in charge of the line. By contrast,
preventative rail grinding aims at keeping rail defects from occur ring,
while adjusting rail contours to achieve maximum locomotive performance
and minimal wear. This type of maintenance does not depend on conventional
visual rail inspections, but is based on the amount of tonnage over a section
of line.
New grinding techniques have not been accepted by the entire industry.
Some railroads have resisted adopting preventative rail grinding practices,
partly because of the high cost of rail grinding. In 1993, the Advanced
Rail Grinding Management Corporation estimated that rail grinding operations
cost between $15,000 and $30,000 per day. Rail roads must carefully weigh
cost savings obtained through better rail profiling against the cost of
per forming preventative maintenance.
Types of Rail Grinders
Rail grinding, like rail defect detection, has long been a service contract
to railroads. Traditionally, large production grinders, along with their
specialized crew, would be hired by a railroad to grind a section of mainline.
The large production grinding trains are largely self-sufficient machines
that carry all the supplies they need to work for days at a time. In recent
years, smaller grinding trains have been developed. These are fully capable
grinders, but designed for smaller- scale jobs and not necessarily intended
for the same type of extended mainline grinding work that the larger trains
do. In some situations, rail ways may purchase these smaller grinder trains
rather than contract their services. The smaller grinding trains are often
used on rapid-transit lines, where it would be impractical to hire a con
tract service because of clearance restrictions and other physical limitations.
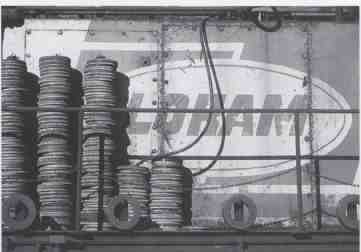
ABOVE: Each grinder has its own circular grinding stone. The stones have
short useful service lives and must be replaced often to provide an optimum
grinding profile. Piles of used grinding stones are stacked along the gangway
of a Loram rail grinder at Cashmere, Washington.
Speno
Speno was a traditional name in rail grinding. Speno provided a contract
rail grinding service to American railroads, and Speno rail grinding trains
were a familiar sight all across the United States.
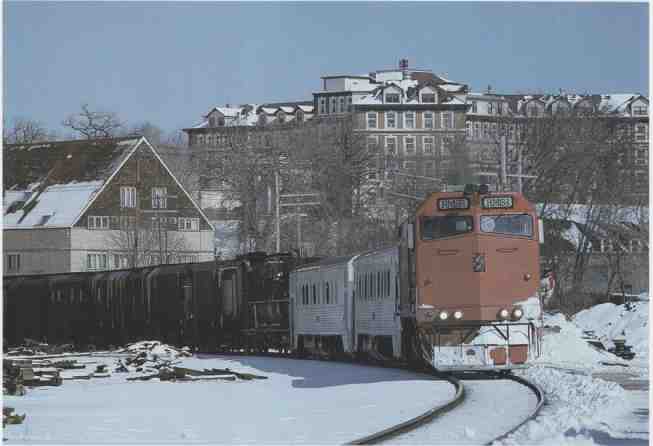
ABOVE: A Speno rail grinder rolls through Waukesha on the Wisconsin Central’s
Chicago to Fond du Lac mainline. One of the most recognized names in rail
grinding, Speno had special locomotives built by Electro-Motive Division.
The RMS-1 rail grinding train used the Optical Rail Wear Inspection System
to analyze track conditions.
One distinctive feature of Speno grinders was that the grinding crew lived
on board the trains in a bunk car as they traveled around. The company
was based in East Syracuse, New York, along the former New York Central
mainline be tween New York and Buffalo. Speno later became part of the
Michigan-based Pandrol-Jackson, which subsequently became a component of
Harsco Track Technologies. While the Speno name no longer appears on American
grinding trains, the company left its mark, literally and figuratively,
on the railroads.
The evolution of modern rail grinders is tied to advances in computer
and visual recording technology, and to changes in railway maintenance
philosophies. In the early 1980s, Speno developed a modern rail grinding
train called the RMS-1 (RMS stands for Rail Maintenance Sys tem). This
train was one of the first to use new electronic optical sensing technology
as part of its pregrinding inspection. The RMS-l’s Optical Rail Wear Inspection
System provided detailed information on the rail profile that allowed for
immediate corrective action by the grinding heads. The recording equipment
was designed to operate anywhere from 2 to 60 miles per hour, which gave
Speno the flexibility to use the system during grinding operations or strictly
as an inspection tool while the train traveled at full speed. The Optical
Rail Wear Inspection System employed a high-speed video imaging system
with a high-intensity flash to project light beams across the railhead,
which were recorded by a special projector. This created a complete image
of the rail profile for analysis. The video system was situated just 3
to 4 inches above the railhead, close enough to gather detailed, accurate
information, but high enough to avoid the normal obstructions that are
part of the track structure. As the RMS-I worked, four different rail images—each
one the product of a different camera—were monitored to assist with the
operation. The out put was recorded both on magnetic tape and as a printout.
The grinder was designed for fail-safe” grinding, to prevent overgrinding
at very slow speeds. If the train suddenly slowed to speeds below the desired
grinding speed, the grinding heads automatically retracted and the grinding
stopped. Overgrinding removes more of the rails than is desired and can
be counterproductive, as overgrinding may shorten rail life rather than
lengthen it.
The RMS-1 was powered by two Electro-Motive Division (EMD) locomotives
specially built for Speno. They incorporated basic components from two
different standard EMD designs, the F4OPH and GP38-2. The Speno locomotive
car- bodies were similar to those used for the F4OPH, EMD’s standard 3,000-horsepower
passenger locomotive introduced in 1976; they are 56 feet, 2 inches long.
Speno made some external modifications to the locomotive cab by extending
the front windows forward to a point almost even with the plane of the
locomotive nose. Unlike the F4OPH, which was powered by a turbocharged
16-cylinder 645E engine that generated 3,000 horsepower for traction, Speno’s
locomotives had the power plant and other components normally used in EMD’s
popular GP38-2 road switcher. This included a normally aspirated 16-cylinder
645E engine that generated just 2,000 horsepower, and standard GP38-2 fuel
tanks. Though EMD considered these locomotives variations of the GP38-2,
they are usually classified as F4OPH-2Ms. Between 1982 and 1985, EMD built
a total of four of these locomotives for Speno. Some rail grinding trains
were powered by former Conrail GP38-2s, which Speno rebuilt and shrouded
with sheet met al at its shops. These peculiar, boxy locomotives are some
of the strangest-looking machines on American rails. Speno’s rail grinding
locomotives carried the train’s RMS designation in the number boards, with
the locomotive number painted on the side of the engine.
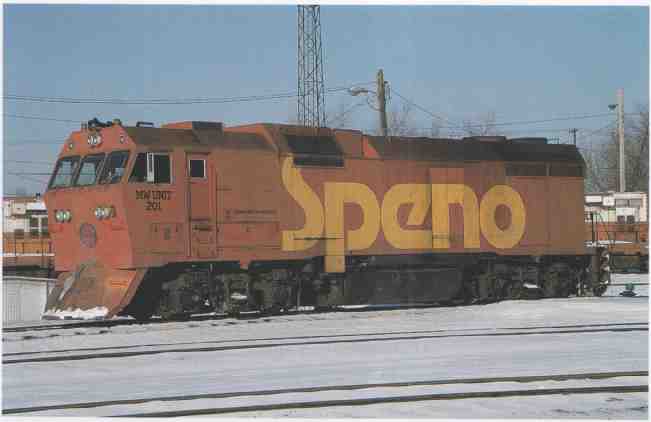
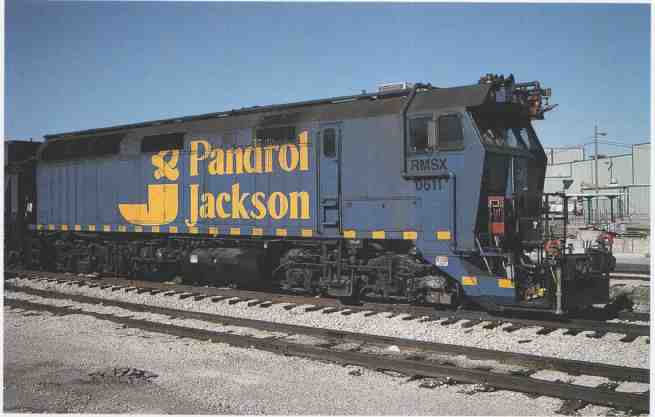
---ABOVE: Speno bought secondhand GP38s from Conrail and remanufactured
them with home-styled car bodies at its East Syracuse shops. When Pandrol-Jackson
inherited Speno’s rail grinding trains, it improved the locomotives’ design
and treated them to a blue-and-yellow paint job.
In 1986, Speno outfitted an even more sophisticated, high-speed production
grinding train, designated RMS-2. It was 625 feet long, comprising 12 cars.
Like the RMS-1, it used a computer system to assist in profiling and grinding
the rails. The onboard computer had up to 99 preprogrammed rail contour
patterns stored in memory, and it was designed for higher productivity
and greater flexibility than earlier machines. Precision automatic sensors
and detailed rail contour pat terns such as those employed on the RMS-2
allow a grinder to shave a minimum amount of steel off the rail. Thus,
a modern computer-controlled grinder is a far more accurate and more efficient
machine than those with a traditional design. Compared to the RMS-1, the
RMS-2 also had easier-to-use computer software applications, which made
running easier for the operators. The train was equipped with 120 rail
grinding heads, each of which was powered by a 20-horsepower electric motor.
The heads were paired in a way to avoid creating long wave form corrugations.
As in other grinders, the stones were attached to a chuck on the motor
to allow for rapid replacement. The RMS-2 was a bidirectional machine,
arranged with a symmetrical consist with locomotives at each end.
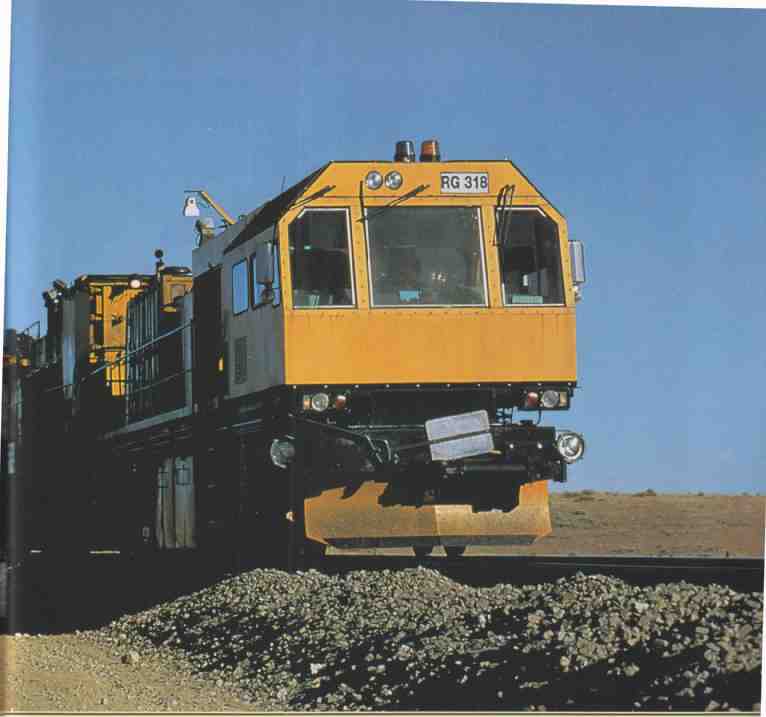
ABOVE: Loram’s sophisticated rail grinder works BNSF’s former Colorado & Southern
line at Trinchera, Colorado. Burlington Northern Santa Fe has a progressive
approach toward rail grinding, working with a preventative plan rather
than the traditional corrective approach. A modern grinder such as this
one is designed to reprofile rail with a single pass.
Among other improvements over the RMS-1, the RMS-2 had more space on board
for crew comfort and storage space for maintenance materials. New crew
cars were designed to keep the crew from being disturbed by the grinding
going on outside. Like other Speno trains, the RMS-2 was self-contained,
allowing it to work for ex tended periods without having to interrupt work
to secure supplies. This feature is particularly important when grinding
on remote sections of track, such as in the American West and in Canada,
where some railroad lines run through hundreds of miles of wilderness and
sparsely settled territory. The train carried 14,000 gallons of fuel on
board, which allowed it to run great distances be tween fuel stops. More
importantly, it carried 44,000 gallons of water to prevent wildfires. Grinding
continually produces hot sparks, and while efforts are made to contain
the sparks, many escape the confines of the machine. Having lots of water
on board is imperative to keep the fire hazard at a minimum.
Speno’s RMS-2 carried a nine-member company crew, including a supervisor,
a foreman, two locomotive engineers, an electronics technician, a cook,
and three support staffers to assist with general work. Rail grinding is
no picnic and requires long working hours by the crew. When the train was
out on the road, the crew might be with the train for months at a time,
living and working in the same fashion as a Sperry rail detector crew.
Pandrol-Jackson
Pandrol-Jackson assumed grinding operations from Speno in the 1990s and
continued to operate the same large grinding trains that Speno had developed,
in addition to its own smaller grinding machines. Where Speno’s trains
were painted a safety orange and yellow, Pandrol-Jackson used a handsome
dark blue-and-yellow scheme for its grinders (though for a time Pandrol’s
trains wore the old Speno colors with Pandrol-Jackson lettering). Pandrol-Jackson
introduced its RMS-5 grinder in 1997, which used many of the fundamental
components of earlier Speno grinders, including the same rebuilt GP38 and
F40PH-2M locomotives. In addition to the two locomotives, the RMS-5 grinder
was composed of nine cars, arranged in the following order: two crew cars,
three grinding cars, two water and fuel storage cars, and two generator
cars. The three grinding cars carried a total of 96 motorized grinding
heads, 48 on each side of the train. Each of these grinding heads was powered
by a 30-horsepower electric motor, and they were angled in place by a hydraulic
control. A grinding command center was situated on the second grinding
car. The dorm and kitchen cars for the crew had been converted from former
GO Transit commuter rail cars from Toronto. The generator cars, which generated
electricity for the grinders, were equipped with a 16-cylinder Caterpillar
diesel engine. The RMS-5 was designed to grind about 80 miles of track
a day, but it had been known to accomplish 20 percent more than that on
very productive days. It used a specially built speed regulator called
a Pace Setter, manufactured by an outside vendor, to maintain precise speed
control when the train was grinding at very slow speeds. One of the locomotives
also powered a dust collection system to minimize environmental damage
from the grinding.
Harsco Track Technologies
Harsco Track Technologies produces several varieties of commercial rail
grinding machines that incorporate the latest advances in rail grinding
technology. The PGM-48 (which stands for Production Grinder, Magnum) mainline
grinder is a self-propelled, self-contained machine designed to produce
optimum-profile rails and remove defects, such as corrugations and rail
lips.
It uses a modern computer network to control and monitor all its grinding
functions and the speed of the machine. This technology allows a single
human operator to oversee the rail grinding procedures. As suggested by
its designation, the PGM-48 has a total of 48 grinder heads, 24 on each
side of the train, which are carried by three grinding cars. They use standard
10-inch grinding stones. The grinding heads are powered by 30-horsepower
motors that turn at speeds up to 3,600 rpm. Two Cummins KTA38 diesel engines
power the train. The PGM-48 is double ended and fully capable of grinding
in either direction at a maximum speed of 15 miles per hour (24 kilometer
per hour). When it isn’t grinding, the train can travel at a top speed
of 50 miles per hour, and can be towed in consist at even faster speeds.
Compared to the older Speno and Pandrol-Jackson grinders, the PGM-48 is
relatively short, measuring only 208 feet (63.43 meters) long. It is 15
feet, 2 inches (4.629 meters) tall.
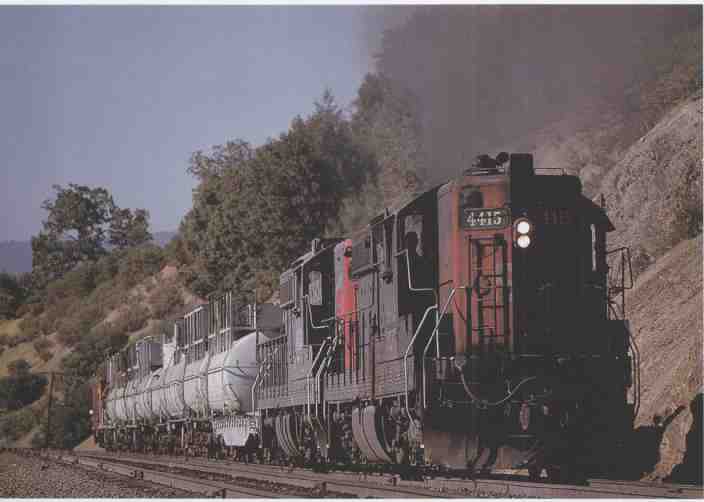
ABOVE: Two venerable Southern Pacific SD9s lead a water train at Long Ravine,
California, in July 1990. The train is making a dash upgrade to Cape Horn
to extinguish a brushfire started by a rail grinder.
Harsco’s PCM-48 grinder is a Cadillac com pared to the dirty, dusty, old-fashioned
grinding trains of days past. Crews work in pressurized, soundproof, climate-controlled
cabins that feature comfortable padded seats. They are designed to provide
the operators with easy access to the controls, while maintaining a clear
view of the tracks. Harsco also manufactures smaller versions of the Magnum
series grinder in configurations of either 16 or 32 grinding motors.
Harsco’s Production Transit Grinder is a smaller machine designed for
lighter jobs. It is a flexible unit intended for both mainline and switch
grinding. It can be configured with 8 to 32 grinding heads. Like the Magnum
series, the Production Transit Grinder has sophisticated modern computer
controls and rail recording systems. Among its other features are a track
vacuum that sucks up particulates left over from the grinding process,
a dust collection system that sucks up airborne particulates (see the RGHC/TVC-A1
system described later), and an obstruction avoidance system.
Harsco’s Model RGHC is a small self-propelled grinder designed for both
domestic and international applications. Although sometimes overshadowed
by the larger production grinding trains, the RGHC is a fully capable modern
grinder. It is suitable for grinding rails in accordance with many different
corrective or preventative profiles. It comes in 8- and 10-stone units,
which may be operated singly or in multiple, de pending on the nature of
the grinding required. This machine is designed to eliminate and pre vent
several common types of rail defects, including long waves, track vibration
corrugations, and millscale.
The RGHC grinder is extremely compact compared to the massive multi-unit
grinders. It measures just 37 feet, 9 inches long; 8 feet, 4 inches wide;
and a little more than 12 feet tall—smaller than the average boxcar traditionally
found on North American railroads. The eight-unit machine weighs 69,500
pounds. The grinder is propelled by a diesel engine with a hydrostatic
transmission system and is capable of a travel speed of 62 miles per hour.
(Why 62 miles per hour? This train is designed for overseas applications
where metric measurements are standard, so while 62 miles per hour seems
like an odd top speed, it converts neatly to the metric equivalent of 100
kilometers per hour.) The grinders are available in fixed standard gauge
versions (4 feet, 8.5 inches) as well variable gauge versions that can
be used on track as narrow as 3 feet, 6 inches (1,067 millimeters), which
is a standard gauge in many countries of the world, including Japan. The
grinding motors are hydraulically powered and work at a maxi mum of 20
horsepower, rotating at between 5,500 and 6,000 rpm. The grinder works
at speeds between 2 and 11 miles per hour, depending on the grinding required.
Like other grinders, the machine is speed sensitive, automatically adjusting
the speed of the motors to compensate for changes in forward velocity,
and thus preventing over-grinding of the rails. It can grind track as steep
as 6 percent, which is about twice as steep as any American mainline.
The grinding motors are located between the driving wheels, below the
body of the machine. They are carefully centered over the rails, with four
grinders per rail. The grinding heads are mounted independently of one
another, allowing for precise adjustment of each grinding stone, as dictated
by the chosen rail profile. The onboard computer can be programmed with
nearly 100 different grinding patterns. The heads are retractable, so they
can be lifted out of the way if there is an obstruction that interferes
with grinding or threatens to damage the equipment. This grinder is specially
designed to grind difficult track sections that other grinders might not
be able to handle well, such as switches, crossings, and highway level
crossings. The rapidly spinning stones are guarded by fire-resistant spark
shields and other equipment specifically designed to keep dangerous sparks
from potentially igniting fires along the tracks. Heat sensors are also
included to warn crew members of excessive heat, alerting them should a
fire start during grinding. When the machine is in operation, water nozzles
douse the tracks with a water mist to keep dust down and minimize the fire
risks. In addition, the grinder has a chemical fire- extinguishing system
and high-pressure hoses with adjustable nozzles for putting out wildfires.
Modern grinders such as the RGHC have much nicer crew cabins than old
fashioned grinders, and compared to the old machines, the control room
on today’s machine seems space- aged. It is pressurized and insulated to
minimize the effects of vibration, noise, and dust, which can be quite
severe on a grinder, yet the cabin has large windows that give operators
a fine view of the tracks. The windows are made from argon-filled double-paned
glass.
Grinding functions on the RGHC are con trolled by an onboard computer.
This computer has to be extremely durable in order to endure the difficult
and potentially damaging conditions imposed by the harsh grinding environment.
Operators direct the grinding on a touchscreen monitor, and the computer
has built-in diagnostic functions to assist operators in event of a failure
or other problems. Since this type of grinder is designed for foreign sales,
the computer is flexible and can be programmed for use in different languages,
making machine operation easier for non-English speakers.
The RGHC grinders can be arranged in a three-car configuration that consists
of two eight- stone grinders bracketing a TVC-AI track vacuum. This machine
creates negative air pressure below the grinders to suck up dust and grinding
debris. The ability to control dust and sparks is one of the most important
attributes of modern grinders outside of their rail profiling functions.
Loram
Loram has been in the rail grinding business for decades. Its mustard
yellow articulated rail grinders are a familiar sight on railroad lines.
Loram’s grinding trains are not as complicated nor as long as the old Speno
trains, in part because the Loram crews do not live on board the trains.
Instead they are housed off-site when they are not working. Loram prides
itself on its high level of crew training, which is more extensive than
that required to meet railroad safety procedures. Since rail grinders have
a propensity to start wildfires, Loram provides its crews with training
in firefighting. Its older grinding trains carried a specially equipped
caboose with firefighting equipment for quickly extinguishing fires ignited
by stray sparks. Like its older trains, Loram’s modern rail grinder is
equipped with a fire prevention and protection system.
Loram recently introduced a modern, sophisticated grinding unit that employs
up-to-date sensing and computer-regulated grinding technology. Through
exhaustive research, Loram developed a rail grinding machine that uses
highly effective computerized rail profile selection, modern grinding stones,
and metal removal. Loram’s rail analysis system, which is known by the
acronym VISTA for ViSion Transverse Analyzer, uses optical technology to
assess rail surface conditions for comparison with remedial surfacing profiles
in preparation for grinding. Loram boasts that its modern grinders are
available to work 98 percent of the time, and its crews often work as many
as 300 shifts a year. Loram grinders operate all over North America and
in several countries around the world.
=== ==
A Day With the Grinder
A typical grinding crew reports for work at 6 A.M. and expects to put
in a full day. In the summer, a grinder sometimes will work at night to
take advantage of the cooler temperatures and naturally forming dew to
help minimize the risk of fire. A grinder may also work at night to avoid
interfering with train schedules, since some lines, particularly those
with heavy suburban passenger traffic, operate most of their trains in
normal daytime hours. Typically, when a grinder is assigned to a line it
may work six days a week, allowing the seventh for rest and maintenance.
Representatives of the railroad ride on board when the grinder is working,
including an official, such as a track superintendent.
Before grinding begins, a plan of action is worked out with the railroad.
Rail profiles need to be selected in advance, and the amount of time the
grinder will have to work on each section of track is decided. Some profiles
can be achieved relatively quickly with just one pass of the machine, while
others require more attention and slower grinding. Deciding which grinding
patterns to use can he quite a complicated business, and this is one area
where the use of sophisticated computers helps considerably.
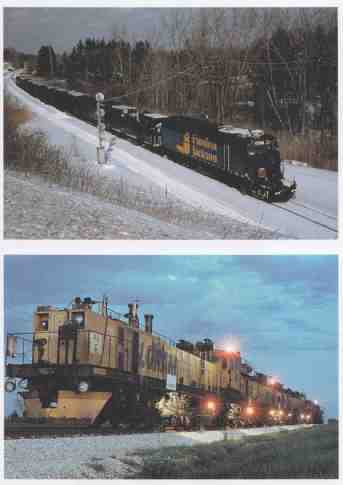
(TOP) Winter is one of the best times to grind rail, since the risk from
brushfires caused by sparks is much lower. On February 1, 2000, a Pandrol-Jackson
rail grinding train rolls through Mechanicville, New York.
(ABOVE) Loram’s
rail grinder No. 6 works at twilight along Southern Pacific’s Dalsa Cutoff
at Caldwell, Texas, on March 29, 1992. This train, outfitted in 1981, has
88 grinders. It was one of more than a dozen Loram grinders in operation
at that time.
== === ===
Water Trains
The fire protection train is one of the more unusual specialty maintenance
trains. These trains date back to 1870, when they were needed to keep the
many miles of wooden snowsheds on California’s Donner Pass from conflagration.
The combination of wooden sheds, sparks from loco motives, and unusually
dry air made for a high fire risk much of the year in the Sierra. Shortly
after the opening of the transcontinental route, fire trains were deemed
a necessity to keep the line open and safe. While Donner Pass was known
for its extraordinary winter weather, which required the snowsheds to begin
with, the high, dry summer and autumn seasons also proved challenging to
railroad operations. At one time, four fire trains were stationed at key
points on the line between Roseville, California, and Sparks, Nevada. These
could be found at Truckee, Summit station, Blue Cañon, and Colfax. Each
train was kept on alert, ready to go at a moment’s notice to fight fires.
The original fire trains consisted of rectangular tank cars hauled by
4-4-0s, including the famous Governor Stanford. The tanks held 7,200 gallons
of water, which were delivered by pumps on the engines at a rate of 150
gallons per minute. By the 1890s, these trains were replaced by even better
ones. They were hauled by 4-6-0s and featured more powerful pumps and head
lights on the tenders to permit quick reversing at night. Central Pacific
maintained several fire lookouts at key locations along its line to watch
for fires. The stations were manned by a telegrapher who could alert the
men on the railroad in the event of a blaze. In the days before telephones
or radio, it was especially important to have a reliable communications
system and a plan of action to deal with an emergency. In to day’s world
of two-way radios, mobile phones, fax machines, and the Internet, it may
be difficult to comprehend how isolated communities were in the nineteenth
century. A fire could be raging out of control between Emigrant Gap and
the Summit, and trains climbing eastward would be oblivious to the problem
until they were practically upon it. Making matters even more serious,
the railroad was covered by shed for more than 30 continuous miles at the
highest elevations. Once a fire got going, it had the potential to be enormously
destructive.
The heyday of the fire train was over by the 1920s. Donner Pass had been
converted to double track, and the railroad was able to eliminate many
of the snowsheds by using large Leslie rotary plows to keep the tracks
clear (see section 7). The fire train did survive into the modern era,
however, to protect the remaining sheds and to minimize the risk from brushfires.
By the 1990s, a water train was called out only on rare occasions, usually
accompanying a rail grinder to both dampen the ground ahead of the grinding
and scamper back to extinguish any fires caused by the grinding sparks.
The modern water train used specially assigned tank cars painted in maintenance-of-way
gray and stenciled “water car.” The cars were equipped with high-pressure
pumps and towed by diesels, usually old GP9s or SD9s.
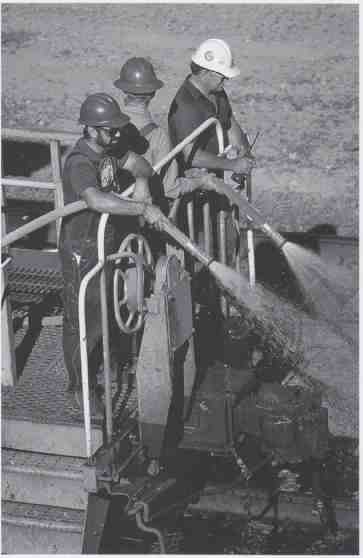
Workers on an SP water train spray down the tracks in advance of
a rail grinder to prevent sparks from igniting wildfires along the tracks.
The water train carries several hundred thousand gallons of water and high-pressure
water cannons, as well as a caboose.
Prev. | Next
Top of Page | Article
Index |